Helicoil Insert |
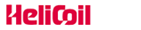 |
|
|
FEATURES AND BENEFITS.. |
Heli-Coil inserts provide a
positive means for protecting and
strengthening tapped threads in any
material. The unique design features
of the insert offer many benefits. |
- Stronger Assemblies
Tapped threads are strengthened
because the inherent flexibility
of the insert provides a more
balanced distribution of dynamic
and static loads throughout the
length of thread engagement.
This flexibility also compensates
for variation in lead and angle
error allowing each coil to carry
its share of the load.
- Corrosion Resistance
Under normal environmental
conditions, Heli-Coil inserts minimize galvanic action
within the threaded assembly
because of their superior
corrosion resistance.
- Design Felxibility
Bolt tensile strength can be
balanced against parent material
shear strength, assuring bolt
failure rather than parent
material damage. Five insert
lengths are available in each
thread size.
- Eliminate Stress
Virtually no stress is introduced
into the parent material
because there is no staking,
locking, swaging or keying in place – the outward spring-like
action of the insert holds it in
place.
- Minimize Space and Weight
Heli-Coil inserts allow use of
smaller bosses, flanges and
fasteners than any other insert.
Heli-Coil inserts can generally
be incorporated in existing
designs, where no provision
has been made for an insert,
without increasing boss size.
- Minimize Total Cost
Cost savings abound. Lower
insert cost, lower installation
cost and Heli-Coil inserts
provide design flexibility by
allowing a wide choice of
parent materials while
maintaining maximum
threaded assembly strength.
- True Clamping Torque
Maximum clamping action and
bolt tension are assured with
minimum wrench torque because
of the mirror-smooth surface
finish of Heli-Coil inserts.
- Wide Temprature Range
Heli-Coil stainless steel inserts
can be used in temperatures
ranging from –320°F to +800°F.
- Quality and Reliability
Stringent Quality Assurance
and Engineering Standards are
rigidly enforced in all phases of
the manufacturing process.
This assures integrity of your
product design.
|
High Production |
Heli-Coil inserts are available
mounted on plastic strips and wound
onto reels (500 or 1000 inserts
per reel). With power installation
tooling, use of strip feed inserts will
substantially increase installation
rates by minimizing handling. |
Universal Acceptance |
Heli-Coil Standard and Screw-lock
Inserts are the original – and have
an extensive background of tension,
torque, shear, vibration and fatigue
tests conducted by American
industry’s leading companies as
well as the U.S. Military. Successful
applications in the fields of aviation,
electronics, industrial, automotive
and military equipment provide a
wealth of experience and confidence
in the performance and reliability of
Heli-Coil inserts. |
Total Design Services |
In addition to the benefits listed
above, Heli-Coil provides a wide
range of support to solve fastening
problems. This manual is one of them
– the following pages are presented
in a manner to make it easy to
“design-in” Heli-Coil inserts to take
advantage of the extraordinary
benefits they provide.
Additionally, our Sales Engineers,
Applications Engineers and
Design Engineers are available for
consultation for specific designs.
When the product gets to the
manufacturing phase, our extensive
experience in production tooling and
installation techniques ensures that
you can indeed make your product
better with Heli-Coil inserts. |
Helicoil screw locking thread inserts |
Locking Features and Benefits.. |
Heli-Coil offers three types of Locking insert for multiple
applications… |
Screw Lock Inserts: |
- Positive self-locking torque,
complying with NASM8846
and MA1565.
- A resilient locking machanism
(applies to Heli-Coil screw-lock
inserts) that grips the bolt and
prevents it from loosening
under vibration or impact.
- Repeated assembly and
disassembly without appreciable
loss of self-locking torque.
- Saving in space, weight and
money, through the elimination
of lock wiring, lock nuts, lock
washers, chemical compounds,
plastic pellets/patches and other
locking mechanisms.
|
High Torque Inserts: |
- Similer to Screw Lock except
higher prevailing torque
compensates for reduced friction
in highly lubricated applications.
- Ideal for higher vibration
applications.
- Approximate 40% increase in
prevailing torque levels.
- Available in #10 through 3/8" UNF only.
- Meets AS1394, AS3094, 3095, 3096, 3097.
|
Stud Lock Inserts: |
- Highest prevailing torque insert
available.
- Enable use of threaded rod for
space-saving stud applications.
- Allows for any class fit of
threaded rod.
- Eliminates inconsistencies caused by interference fit studs.
- Available for both straight and step studs, #10 through 1/2"
UNC and UNF.
- Meets AS1229, AS3080, 3081, 3082, 3083
|
Industry Standards
Heli-Coil inserts and tooling comply with the following Standards and Specifications: |
- NASM122076 thru NASM122275.
Insert, corrosion resistant
Helical Coil Coarse Thread(Inch Series).
- NASM124651 thru NASM124850.
Insert, corrosion resistant
Helical Coil Fine Thread (Inch Series)
- NASM21209. Insert, Screw Thread - Self Locking (Inch Series)
- NASM8846. Insert, Screw Thread, Helical Coil
- MA1565. Insert, Screw Thread, Helical Coil (Metric Series)
- MA1567. Insert, Screw Thread, Helical Coil (Metric Series), Standard Dimensions, Assembly
- MA3279, 3280, 3281. Insert, Screw Thread, Helical Coil, Free Running(Metric Series)
- MA3329,3330,3331. Insert, Screw Thread, Helical Coil, Screw Locking(Metric Series)
- AS59158. Tools for inserting and extracting Helical Coil Inserts.
- NAS1130. Insert, Screw Thread, Helical CoilFree Running and Screw Locking(Inch Series)
|
Helicoil Industry Standard |
- FED-STD-H28.Screw Thread Standard for Fedral/Services
- AS1394 thru 3097
- AS1229 thru 3083 Special Locking Torque Inserts
- ASMEB18.29.1 Insert, Screw
Thread, Helical Coil (Inch Series)
- ASME B18.29.2M-2005 Helical Coil Screw Thread Inserts, Free Running and
Screw Locking (Metric Series)
- AGS3600-3699 Insert, Screw
Thread, Screw Locking, Helical
Coil, Cadmium Plated (Inch
Series)
- AGS4677 Series Insert, Screw
Thread, Screw Locking, Helical
Coil, Cadmium Plated (Metric
Series)
- AS6733 Inserts, Wire Thread,
(UNF) - Unplated
- AS6734 Inserts, Wire Thread,
(UNC) - Unplated
- AS8455 Inserts, Wire Thread,
(UNF) - Cadmium Plated
- AS8456 Inserts, Wire Thread,
(UNC) - Cadmium Plated
|
Helicoil Insert coatings & plating |
Coating/Plating |
Benefits |
Dry Film Lubricant |
Provides additional lubrication in high friction applications
High temperature resistance (400°F)
Highly recommended with Heli-Coil Screw-Lock inserts
Mildly corrosion resistant
Material Spec. AS5272 Color . Grey |
Cadmium Plating |
Provides high corrosion resistance
Provides lubrication to prevent galling
(Not recommended for new design due to its toxic nature)
Material Spec. QQ-P-416-TYPE-II
Color: Iridescent yellow - Free-Running
Color: Olive drab - Screw-Lock
|
Primer - Free II |
Contains no chromates
Free Eliminates need for zinc primers and epoxies
Prevents galvanic corrosion between insert and parent material
Eliminates locking torque issues associated with primers
Improves installation productivity
Provides additional lubrication facilitating insert installation
Material Spec:None
Color : Matte Black |
Silver Plating |
Recommended to reduce galling of threads at high temperatures
For use up to 1200ºF |
Color Coding |
Facilitates verification of insert installation
Coding Allows for quick identification of similar size inserts
Available in blue, green, red, and black* |
|
* All Heli-Coil Inch Screw-Lock inserts are supplied with a red coloring in accordance with NASM21209. |
Helicoil insert Materials |
Heli-Coil inserts are available in a wide choice of materials to suit specific application needs.
Contact Heli-Coil Applications Engineering to determine the correct material for your specific application. |
- Standard, General purpose
material
- Stocked in most size
- Ideal for original equipment application, repair and overhaul.
|
Inconel v750 |
- Used in areas exposed to high
temperatures
- Typical Uses : gas turbine
engines, nuclear applications,
well drilling
- Non Magnetics.
|
Phosphor Bronze |
- Ideal for salt water application
- Non magnetic
- Exellent electrical conectivity
|
Nitronic 60 |
- Superb gall resistance.
- Compatible with stainless steel screws
- Ideal for use in vacuum environment
- Required no addional coating or Plating
- Particle Free
- non megratic
|
Titanium |
- suprior strength to weight ratio
- Corrosion resistant
- Excellent low temperature stability.
|
Helicoil screw lock torque data |
Heli-Coil Screw-Lock inserts meet
the locking torque value of Tables
I and II shown below. The values
shown conform to NASM8846 (inch
series) or MA1565 (metric series)
requirement. |
TABLE 1. Heli-coil Insert Locking Torque - Inch |
Thread Size |
Max Locking Torque |
Min. Locking Torque 15th Cycle |
INCH COARSE THREAD (UNC) |
1(.073)-64 |
15 oz-in |
2 oz-in |
2(.086)-56 |
20 oz-in |
3 oz-in |
3(.099)-48 |
32 oz-in |
7 oz-in |
4(.112)-40 |
48 oz-in |
10 oz-in |
5(.125)-40 |
75 oz-in |
13 oz-in |
6(.138)-32 |
6 lb-in |
1.0 lb-in |
8(.164)-32 |
9 lb-in |
1.5 lb-in |
10(.190)-24 |
13 lb-in |
2.0 lb-in |
12(.216)-24* |
24 lb-in |
3.0 lb-in |
1/4(.2500)-20 |
30 lb-in |
4.5 lb-in |
5/16(.3125)-18 |
60 lb-in |
7.5 lb-in |
3/8(.3750)-16 |
80 lb-in |
12.0 lb-in |
7/16(.4375)-14 |
100 lb-in |
16.5 lb-in |
1/2(.5000)-13 |
150 lb-in |
24.0 lb-in |
9/16(.5625)-12 |
200 lb-in |
30.0 lb-in |
5/8(.6250)-11 |
300 lb-in |
40.0 lb-in |
3/4(.7500)-10 |
400 lb-in |
60.0 lb-in |
7/8(.8750)-9 |
600 lb-in |
82.0 lb-in |
1(1.000)-8 |
800 lb-in |
110.0 lb-in |
1-1/8(1.1250)-7 |
900 lb-in |
137.0 lb-in |
1-1/4(1.2500)-7 |
1000 lb-in |
165.0 lb-in |
1-3/8(1.3750)-6 |
1150 lb-in |
185.0 lb-in |
1-1/2(1.5000)-6 |
1350 lb-in |
210.0 lb-in |
INCH FINE THREAD (UNF) |
2(.086)-64 |
20 oz-in |
3 oz-in |
3(.099)-56 |
32 oz-in |
7 oz-in |
4(.112)-48 |
48 oz-in |
10 oz-in |
6(.138)-40 |
6 lb-in |
1.0 lb-in |
8(.164)-36 |
9 lb-in |
1.5 lb-in |
10(.190)-32 |
13 lb-in |
2.0 lb-in |
1/4(.2500)-28 |
30 lb-in |
3.5 lb-in |
5/16(.3125)-24 |
60 lb-in |
6.5 lb-in |
3/8(.3750)-24 |
80 lb-in |
9.5 lb-in |
7/16(.4375)-20 |
100 lb-in |
14.0 lb-in |
1/2(.5000)-20 |
150 lb-in |
18.0 lb-in |
9/16(.5625)-18 |
200 lb-in |
24.0 lb-in |
5/8(.6250)-18 |
300 lb-in |
32.0 lb-in |
3/4(.7500)-16 |
400 lb-in |
50.0 lb-in |
7/8(.8750)-14 |
600 lb-in |
70.0 lb-in |
1(1.000)-14* |
800 lb-in |
92.0 lb-in |
1(1.000)-12 |
800 lb-in |
90.0 lb-in |
1-1/8(1.1250)-12 |
900 lb-in |
117.0 lb-in |
1-1/4(1.2500)-12 |
1000 lb-in |
143.0 lb-in |
1-3/8(1.3750)-12 |
1150 lb-in |
165.0 lb-in |
1-1/2(1.5000)-12 |
1350 lb-in |
190.0 lb-in |
|
|
TABLE II. Heli-Coil Insert Locking Torque – Metric |
Thread Size |
Max. Locking Torque N.m |
Min. Locking Torque 15th Cycle N.m |
METRIC COARSE |
M2x0.4 |
0.12 |
0.003 |
M2.2X0.45 |
0.14 |
0.02 |
M2.5X0.45 |
0.22 |
0.06 |
M3X0.5 |
0.44 |
0.1 |
M3.5X0.6 |
0.68 |
0.12 |
M4X0.7 |
0.9 |
0.16 |
M5X0.8 |
1.6 |
0.3 |
M6X1 |
3 |
0.4 |
M7X1 |
4.4 |
0.6 |
M8X1.25 |
6 |
0.8 |
M10X1.5 |
10 |
1.4 |
M12X1.75 |
15 |
2.2 |
M14X2 |
23 |
3 |
M16X2 |
32 |
4.2 |
M18X2.5 |
42 |
5.5 |
M20X2.5 |
54 |
7 |
M22X2.5 |
70 |
9 |
M24X3 |
80 |
11.0 |
M27X3 |
95 |
12 |
M30X3.5 |
110 |
14 |
M33X3.5 |
125 |
16.0 |
M36X4 |
140 |
18.0 |
M39X4 |
150 |
20.0 |
METRIC FINE |
M8X1 |
6 |
0.8 |
M10X1 |
10 |
1.4 |
M10X1.25 |
10 |
1.4 |
M12X1.25 |
15 |
2.2 |
M12X1.5 |
15 |
2.2 |
M14X1.5 |
23 |
3 |
M16X1.5 |
32 |
4.2 |
M18X1.5 |
42 |
5.5 |
M20X1.5 |
54 |
7 |
M22X1.5 |
70 |
9 |
M18X2 |
42 |
5.5 |
M20X2 |
54 |
7 |
M22X2 |
70 |
9 |
M24X2 |
80 |
11.0 |
M27X2 |
95 |
12 |
M30X2 |
110 |
14 |
M33X2 |
125 |
16.0 |
M36X2 |
140 |
18.0 |
M39X2 |
150 |
20.0 |
M36X3 |
140 |
18.0 |
M39X3 |
150 |
20.0 |
|
|
|
* These sizes are not included in NASM8846. Torque values shown are interpolated from sizes that are included. All torque data derived for stainless inserts only. |
Helicoil Design Data |
Assembly Strength
Heli-Coil offers maximum design
flexibility while adhering to conservative
engineering practice allowing use
of Heli-Coil inserts in virtually any
application or material. Five lengths
of inserts are available. In this design
manual, the lengths are listed as
multiples of the nominal thread diameter of the screw 1,1.1,2,2-1/2, and 3.
This choice of insert length balances
the bolt tensile strength against the
shear strength of the parent material.
This allows for the design of assemblies
where the bolt will fail before the parent
material. Tables III and IV below show
the length of insert to be used with
different combinations of bolts and
parent materials |
Shear strength of parent material(PSI)
(Alum.,Mag,Steel) |
Table III - Inch Bolt & Heli-Coil Insert Selection Guide
Bolt Material Minimum Ultimate Tensile Strength(PSI) |
54,000 |
75,000 |
96,000 |
108,000 |
125,000 |
132,000 |
160,000 |
180,000 |
220,000 |
10,000 |
2 |
2-1/2 |
3 |
3 |
- |
- |
- |
- |
- |
15,000 |
1-1/2 |
1-1/2 |
2 |
2-1/2 |
2-1/2 |
3 |
3 |
- |
|
20,000 |
1 |
1-1/2 |
1-1/2 |
2 |
2 |
2 |
2-1/2 |
3 |
3 |
25,000 |
1 |
1 |
1-1/2 |
1-1/2 |
1-1/2 |
2 |
2 |
2-1/2 |
2-1/2 |
30,000 |
1 |
1 |
1 |
1-1/2 |
1-1/2 |
1-1/2 |
2 |
2 |
2-1/2 |
40,000 |
1 |
1 |
1 |
1 |
1 |
1-1/2 |
1-1/2 |
1-1/2 |
2 |
50,000 |
1 |
1 |
1 |
1 |
1 |
1 |
1 |
1-1/2 |
1-1/2 |
|
Shear strength of parent material(PSI)
(Alum.,Mag,Steel) |
Table IV - Inch Bolt & Heli-Coil Insert Selection Guide
Bolt Material Minimum Ultimate Tensile Strength MPa(megapascals) |
300 |
400 |
500 |
600 |
800 |
1000 |
1200 |
1400 |
70 |
1.5 |
2 |
2.5 |
2.5 |
- |
- |
- |
- |
100 |
1 |
1.5 |
1.5 |
2 |
2.5 |
3 |
- |
- |
150 |
1 |
1 |
1.5 |
1.5 |
2 |
2 |
2.5 |
3 |
200 |
1 |
1 |
1 |
1 |
1.5 |
1.5 |
1.5 |
2.5 |
250 |
1 |
1 |
1 |
1 |
1 |
1.5 |
1.5 |
2 |
300 |
1 |
1 |
1 |
1 |
1 |
1.5 |
1.5 |
1.5 |
350 |
1 |
1 |
1 |
1 |
1 |
1 |
1.5 |
1.5 |
|
|
Type of Conditions & Protective Methods |
Parent Material |
Parent Material treatment |
Insert Treatment |
Aluminum
Magnesium |
Normal |
Severe |
Extremely Severe |
None |
1 |
1 |
1 |
1 |
1 |
|
Normal |
Severe |
Extremely Severe |
None |
2 or 3 |
2 or 3 |
None |
2 or 3 |
2 or 3 |
|
|
Corrosion Protection Methods |
Method 1 - Parent Material Protection
Aluminum: For oxide coating use Alodine, Anodize, Iridite, Hard Coat or equivalent. Iridite 14 or 14-2 (MIL-C-5541) is recommended for critical parts rather than anodizing
(MIL-S-5002).
MAGNESIUM: For oxide coating use Iridite 15 or dichromate surface treatments. For HAE finishes, always plug tapped holes first.
Method 2 - Coat the insert with one of the following:
Cadmium per QQ-P-416, Type II, .0001" thick; or Dry Film Lubricant per AS5272 (MIL-L46010)(no graphite.)
Methode 3 - Utilize Heli-Coil Primer-Free II coated inserts or seprate the parent material from the insert by using liquid zinc chromate primer, Federal Specification TT-P-1757.Apply the primer to the hole sparingly and install the insert while the primer is still wet.
In addition to the above methods, further corrosion protection can be achieved by:
- Using blind holes wherever possible.
- Using a sealing, insulating or step-down(5052 Alum.) washer under the head of the bolt.
- using bolts that extend completely through the length of the insert.
- In critical applications, using a non-harening sealer or compound on the threaded assembly.
|
helicoil, helicoil insert, helicoil inserts, heli-coil, , NASM21209,MS21209 ,NASM33537,MS33537 ,MS122076 to MS124831,NAS1130, LN9039,LN9039A, LN9499 ,LN9499A,DIN8140, MS122076 to MS124831,MA3279 ,MA3280 ,MA3281 ,MA3329 ,MA3330 ,MA3331, SAE8879, BACi12AE,AGS3600, AGS3700, AGS4677, AS6733, AS6734 , AS8455 ,AS8456 ,AS3094 AS3095,AS3096, AS3097, GE N926, N926A ,N926B ,N926C |
|
Download Product Catalogues |
|
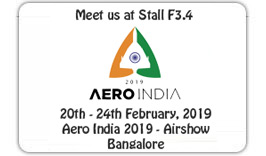 |
|
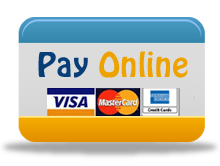 |
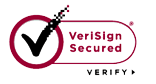 |
|
|