Somta Thread Cutting Taps |
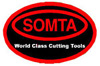 |
|
|
A large variety of Thread cutting Taps - Hand taps, Machine taps & Fluteless taps are available in following materials & special coatings.
Materials
Somta Taps are manufactured from the finest steel available. The heat treatment process is controlled by our metallurgical laboratory using advanced computerised and electronic instrumentation. High Speed Steel contains various elements such as Molybdenum, Tungsten, Cobalt and Vanadium and must be specially treated to produce the ideal combination of strength, toughness and wear resistance. Somta products are manufactured from one of the following High Speed Steels depending on the product and application.
M2 is the standard High Speed Steel and is used where toughness is important, together with a good standard of wear resistance and red hardness.
M35 is a development of M2 and contains 5% cobalt which gives improved hardness, wear resistance and red hardness. It may be used when cutting higher strength materials.
M42 can be heat treated to very high hardness levels of up to 70 HRC (1 000 HV) although normally a slightly lower figure will be employed to retain toughness. The steel is ideal for machining higher strength materials and work hardening alloys such as stainless steels, nimonic alloys etc. Despite its high hardness, M42 has good grindability characteristics due to a lower vanadium content.
M9V material is mainly used in the manufacture of machine taps because of its good wear resistance, good grinding capabilities, high hardness and excellant toughness.
Coatings
Bright Finish
A bright finish has no surface treatment and is suitable for general purpose use.
Blue Finish
A blue finish is achieved by steam tempering - a thermal process which imparts a non-metallic surface to the tool. This surface is porous and by absorbing lubricant, helps prevent rusting, reduces friction and cold welding, resulting in increased tool life. Steam tempered products can successfully be used at slightly increased machining rates or on more difficult to machine materials.
Gold Oxide
This is a metallic brown coloured surface treatment achieved by a low temperature temper and is normally only used on cobalt products for identification purposes
Nitriding
Nitriding imparts a hard surface to the tool and is used for prolonging tool life and machining difficult to machine materials. Because nitriding makes the edge more brittle, care must be exercised in the type of application Nitrided tools are normally also steam tempered.
Titanium Nitride Coating (TiN)
TiN coating is a very hard, gold coloured surface coating a few microns thick which is applied by means of a complex process, called Physical Vapour Deposition (PVD), by advanced modern equipment. The coating is non-metallic and therefore reduces cold welding.
In certain applications increased speed and feed rates can be achieved because of:
a. The hardness of the coating.
b. The reduction in cutting force required due to a decrease in friction between the tool and the workpiece. Tool performance will deteriorate after re-sharpening.
Titanium Carbonitride(TiCN)
The addition of carbon to TiN results in a significant increase in the hardness of TiCN over TiN. TiCN also has a much lower coefficient of friction which enhances the surface finish of components machined with TiCN coated tools, higher productivity can be achieved on a wide range of materials but, in particular stainless steel, titanium and nickel based alloys.
Titanium Aluminium Nitride(TiALN)
In addition to a higher hardness than both TiN and TiCN the aluminium in the coating imparts a much greater oxidation stability. This is as a result of a very thin film of (Aluminium Oxide) being formed on the surface of the TiALN. The film is self repairing, leading to additional increased service life. These improvements allow the coating to withstand much higher temperatures which in turn allows increased cutting conditions, especially usefull when machining Cast Iron and tough steels. |
|
|
|
PREMIUM RANGE OF SOMTA COLOR BAND MACHINE TAPS FOR SPECIFIC APPLICATIONS |
|
|
BLUE BAND MACHINE TAP |
|
|
|
Stainless steels are used extensively for components and products that demand corrosion resistance and long life. The machining of stainless steels is difficult due to its work hardening properties, toughness and poor thermal conductivity, which places high demands on the cutting tools. The Blue band has been specifically adapted to suit these difficult machining requirements.
-
BLUE BAND TAP CHARACTERISTICS
• Thread and flute configuration designed for tough materials, such as Stainless Steel,
Titanium Alloys, Cast Steel, Heat Resisting Steel and Work Hardening Steel.
• HSSE - Vanadium content for toughness.
• Truncated Thread - Truncated thread after lead reduces frictional contact with the threaded hole and allows easier penetration of coolant.
• Material Properties - Used to tap materials with hardness up to 350HB, tensilestrength up to 1250N/mm sq.
• Surtace Finish - TiAIN coating increases surface hardness of the tool to around 87Rc with an excellent hot hardness working temperature and high oxidation temperature making it suitable for dry machining.
|
|
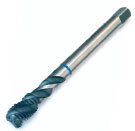 |
|
|
GREEN BAND MACHINE TAP |
|
The machinability of different steels is just as varied as their properties. Soft-tough construction steels place completely different demands on the tools and the green band combination of taps and drills has been perfected for this range of steels.
|
|
GREEN BAND TAP CHARACTERISTICS
|
|
• HSSE- Vanadium content for toughnessM
• Thread and flute configuration design for free cutting and structural steels in the general purpose range of medium tensile strength.
• Used to tap material with hardness up to 250HB, tensile strength up to 900N/mm Square.
• TiN Coating increases surface hardness to 85Rc, with excellent resistance to abrasion and cold welding.
|
|
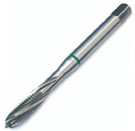 |
|
|
RED BAND MACHINE TAP |
|
The mechanical properties of materials are influenced diversely by the addition of alloying elements and heat treatment processes, resulting in some high-strength, quenched and tempered steels or hardened steels. This range has its own unique set of machining requirements which are satisfied by the red band range of taps.
|
|
RED BAND TAP CHARACTERISTICS |
• HSSE - Vanadium content for toughness
• Thread and flute configuration designed for high tensile materials such as Tool Steels, Heat
Treatable Steels, Spring Steel, Case Hardening Steel, Unalloyed Titanium, Nitriding Steel, Cold Drawn Constructional Steel and High Tensile Steel.
• Used to machine materials with hardness up to 470HB, tensile strength up to 1500N/mm square.
• TiAlN coating increases surface hardness of the tool to arount 87Rc with an excellent hot hardness working temperature and high oxidation temperature making it suitable for dry machining.
|
|
 |
WHITE BAND MACHINE TAP |
|
|
|
Having damping and thermal conductivity, with high strength and resistance to wear characteristics, Cast Iron is a material that is used extensively for mass produced components which all require machining. The SOMTA white band range of taps has been designed to suit this demand. |
|
WHITE BAND TAP CHARACTERISTICS |
|
• Designed for highly abrasive material such as Cast Iron and reinforced plastics.
• Increased number of flutes reduces torque and increases tap life.
• Used to tap material with hardness up to 300HB, tensile strength up to 1000N/mm square.
• TiAlN coating increases the surface hardness of the tool to around 87Rc with an excellent hot hardness working temperature and high oxidation temperature making it suitable for dry machining. |
|
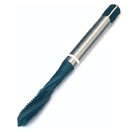 |
|
|
YELLOW BAND MACHINE TAP |
|
|
|
The alloying elements which achieve varying Aluminium Alloys have an effect on themachining properties of these materials. This generally creates a difficult chip formation and material which has tendencies to stick to the tool, placing very different demands on the tool. The yellow band contends with these machining difficulties.
|
|
YELLOW BAND TAP CHARACTERISTICS |
|
• Flute and Thread designed for more ductile materials such as Aluminium, Magnesium Alloys, Soft Brass (MS58), Plastic, Zinc Alloys and Copper.
• Flutes - Wide flutes allow more efficient swarf removal which prevents clogging and torque build-up.
•
Rake Angle - High rake angle improves shear characteristic and reduces build-up on the cutting edge, allowing tap to cut more freely for longer periods.
•
Surface Finish - Bright as ground condition which is the most suitable finish forthis ductile range of products.
•
Material Properties - Used to tap materials with hardness up to 200HB, tensile strength up to 700N/mm square.
•
FLUTE - 35° helix. open profile designed for efficient swart evacuation. |
|
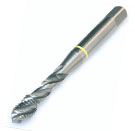 |
Thread cutting tool, thread cutting tools, thread cutting tap, thread cutting taps, hand tap, hand taps, hand tap set, hand tap sets, machine tap, machine taps, spiral fluted machine tap, spiral fluted machine taps, spiral pointed machine tap, spiral pointed machine taps , dormer tap, emuge tap , dormer taps, emuge taps, fraisa tap, fraisa taps, somta tap, somta taps , thread forming tap, thread forming taps, thread rolling tap, thread rolling taps,totem tap, totem taps, totem hand tap, totem machine tap |
|
|
|
Download Product Catalogues |
|
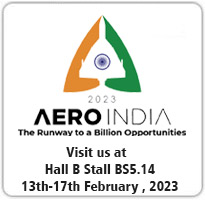 |
|
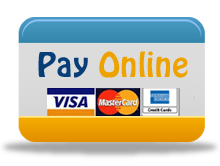 |
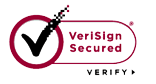 |
|
|